半導体のプロセスは半導体チップを製造する前工程と,その後のパッケージ化などをする後工程に分かれます.本記事では前工程について解説していきます.
そのほかの電子回路やプロセス技術は下記からたどることができます。
半導体製造装置
前工程の解説の前に簡単に半導体製造装置について説明します.半導体の各工程では半導体製造装置が必要になります.半導体製造装置は高度な技術が必要で,市場としては寡占状態になりやすいです.
半導体製造装置は大きく分けてバッチ式と枚葉式があります.バッチ式と枚葉式の2つのタイプでは処理する方法なども異なります.
バッチ式は数十枚などの多数のウェーハをまとめて処理することができます.そのため,大量に製造したい場合はより安価に処理することができます.枚葉式はウェーハを1枚ずつ処理していくタイプです.枚葉式はより省スペースかつより柔軟な処理ができるメリットがあります.また数枚程度をまとめて枚葉式で処理する多枚葉式もあります.
前工程・フロントエンド (FEOL)
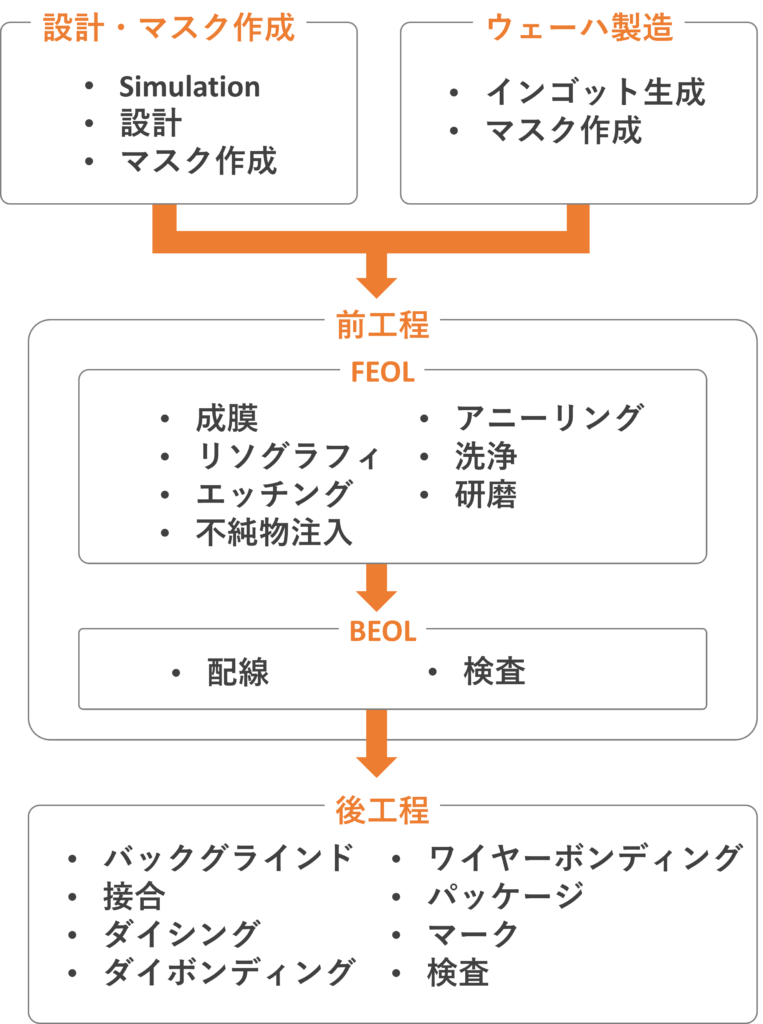
半導体チップの製造工程はウェハに回路などを形成する前工程と,チップを切り取って組み立てる後工程に分けられます.前工程はさらにトランジスタ形成までのフロントエンド (FEOL: Front End Of Line)と,それ以降の配線形成をするバックエンド (BEOL: Back End Of Line)に分けられます.
FEOLとBEOLでは熱処理の温度が違います.FEOLではシリコン中の欠陥をなくしたり,不純物をうまく拡散させるために高い温度が使われます.それに対してBEOLでは金属が使われ,温度耐性がシリコンと比べて高くないため,FEOLのときほど高い温度を使えない違いがあります.
成膜
成膜技術はウェーハに金属や絶縁体などの様々な材料の薄い膜を形成する技術です.以下に様々な成膜の方法とそれぞれの特徴を示します.
成長の分類 | 種類 | 成膜方法 | 説明 |
---|---|---|---|
固相成長 | 熱酸化膜 | 1000℃近い高温でウェーハを加熱して,Si表面を酸化させることで酸化膜 (SiO2)を形成する方法です.ウェーハ表面のSiが材料となるため,表面Siが少し薄くなり,代わりに2.27倍程度の厚さの酸化膜ができます. | |
気相成長 | CVD (ドライ工程) | CVD (Chemical Vaper Deposition,化学的気相成長)はガス (気相)を用いて化学的な反応を利用して成膜する方法です.化学反応には以下のように熱,光,プラズマなどが利用されます.基板とガスによって成膜させる物質が変わります.大がかりな真空装置が必要ない,成膜速度や処理面積が広い,構造体での成膜がより均一に形成可能 (Step Coverageがいい)な特徴を持ちます.CVDには熱CVD,プラズマCVD,光CVD,MOCVD,ALDなどがあります. | |
ALD | ALD (Atomic Layer Deposition,原子膜蓄積)は2種類以上のガスを交互に注入していくことで,原子レベルの成膜が可能な手法です. | ||
PVD (ドライ工程) | PVD (Physical Vapor Deposition,物理的気相成長)は物理的な力で成膜を形成します.PVDは真空蒸着,スパッタリング,イオン化蒸着,イオンビームに大別されます. | ||
真空蒸着 | 真空蒸着は真空によって材料を蒸発させて成膜させる方法です.蒸発のための加熱は抵抗による発熱と電子ビームによる発熱の方法があります. | ||
スパッタリング | スパッタリングは真空にしたチャンバー内にガスを導入し,電界によって加速されたガスをターゲット (成膜させる材料)に衝突させて材料を飛びださせて,ウェーハに成膜させる技術です.精度が高く,Step Coverageに優れています. | ||
イオン化蒸着 | 真空で加熱して材料を蒸発させ,蒸発した材料をイオン化して材料に成膜させます.他のPVDと比較して密着性が高いです. | ||
エピタキシャル成長 | エピタキシャル成長はウェーハ上 (基板上)に新たに単結晶を成長させる成膜方法です.基板と同じ材料であればホモエピタキシャル成長,異なる材料であればヘテロエピタキシャル成長といいます. | ||
液相成長 | 塗布 (ウェット工程) | 塗布は液相を用いて成膜させます.レズストの成膜は塗布の一種であるスピンコート法によって行われます. | |
メッキ (ウェット工程) | 銅などのCVPやPVDによる薄膜が難しい金属では,薬液を用いて金属をメッキさせます.銅配線はメッキで金属を堆積させて,余分な金属を削って配線を作るダマシンプロセスが利用されます. |
有名な成膜装置の製造メーカーとしてはAMAT (Applied Materials) (アメリカ),Lam Research (アメリカ),東京エレクトロン (TEL) (日本)があります.
フォトリソグラフィ
フォトリソグラフィ (リソグラフィ)は光の照射などによって,回路パターンを描く工程です.フォトリソグラフィの工程は以下のように行われます.
- ウェーハの洗浄
- レジスト塗布:スピンコート法でレジストを設定した厚さに均一に成膜します.
- プリベーク :レジストの溶剤を蒸発させてレジストを密着させます.
- 露光 :フォトマスクの上から光を照射して回路パターンを照射します.
- 現象・リンス:現象で余分なレジストをなくします.露光で光を照射した箇所が現象液で溶けるポジ型と光を当てた箇所が現象液で溶けなくなるネガ型があります.微細に有利なポジ型が主流です.現象後はリンス液 (純度の高い水)で洗浄します.
- ポストベーク
- (エッチングや不純物注入)
- レジスト除去 (アッシング)・洗浄
その他のリソグラフィや露光装置の特徴を以下に示します.
- 露光装置のシェアのほとんどはASML (Advanced Semiconductor Materials Lithography) (オランダ).
- 他の露光装置製造会社にはニコン (日本)やキャノン (日本)がある.
- 露光装置は非常に高価.
- リソグラフィ技術の進化は集積回路の微細化に大きく関係.
- 露光装置には使う波長によってi線 (波長:365 nm程度),KrF (波長:248 nm程度),ArF,EUV (波長:13.5 nm程度)がある.
- 液浸リソグラフィによってより微細な加工が可能になった.
- 波長が短いほど微細な加工が可能だが,EUVを用いた露光装置製造には高度な技術が必要.
エッチング
エッチングはウェーハ表面の一部分を取り除く工程です.エッチングには薬液を使ったウェットエッチングとガスやプラズマを利用したドライエッチングがあります.一般に,ウェットエッチングは等方性エッチングでレジストの下までえぐれてしまいます.それに対してドライエッチングは異方性エッチングで,レジスト下はあまりえぐれずにきれいにエッチングすることができるため,集積チップの加工はドライエッチングが主流となっています.
エッチング装置で高いシェアを持つ会社はLam Research (アメリカ),東京エレクトロン (TEL) (日本),AMAT (Applied Materials) (アメリカ)があります.
不純物注入
不純物注入 (イオン注入,ドーピング)はウェーハに不純物を注入する工程です.不純物を注入することでN型半導体やP形半導体の層を形成させることができます.イオン注入は以下のように構成されます.
- イオンソース:不純物イオンを生成させる
- 質量分離 :質量の違いを利用して,必要ないイオンを除去させる
- 分析スリット:必要なイオンのみを通すためのスリット
- 加速部 :不純物イオンを加速させる
- 偏向器 :イオン注入の精度を上げるために偏向させる
- Qレンズ :イオンを絞る
- 走査部 :不純物イオンを照射させる方向を走査しながら不純物イオンを照射する
不純物の注入後はダメージが増えるため,アニール (熱処理)によってダメージを回復させます (熱処理によって不純物は拡散してしまうことに注意).また熱処理によって不純物を拡散させてSiと結合させることでドナー・アクセプタとして機能させます (活性化).
イオン注入はイオンの種類,注入させる深さ (注入させるときのエネルギー),濃度 (電流×時間),注入する角度の制御が可能です.イオン注入では金属汚染,ダメージ,横方向での広がりなどを気にする必要があります.
不純物の注入にはイオン注入,固相拡散,気相拡散,プラズマドーピング,レーザードーピングなどの種類があります.有名なイオン注入装置製造会社としては住友重機械イオンテクノロジー (日本)やAMAT (Applied Materials) (アメリカ)があります.
アニール (熱処理)
アニールは、半導体製造プロセスにおける熱処理工程で、シリコンウェハやチップを特定の温度に加熱し、冷却することで材料の特性を改善する作業です。このプロセスは、主に不純物の拡散を制御したり、結晶構造を改善したり、ストレスを解消したりする目的で行われます。
アニールにはさまざまな目的がありますが、最も一般的なのは、イオン注入後に行われるアニールです。イオン注入では、不純物をシリコンウェハに打ち込むことによって、特定の電気的特性を持たせますが、その後にアニールを行うことで、注入された不純物を所定の位置に定着させ、シリコンの結晶構造を修復します。また、アニールはウェハの内部応力を緩和し、材料の強度や耐久性を向上させる役割も果たします。
アニールの温度や時間は非常に重要で、適切な条件を選ぶことで望ましい特性を持つ半導体デバイスを製造することができます。温度が高すぎると、逆に材料が劣化することもあるため、精密な管理が必要な工程です。
アニール装置の種類としてはバッチ式であるホットフォール型や,枚葉式であるRTA (Rapid Thermal Anneal)やレーザーアニールがあります.
研磨 (ポリッシング)
研磨 (ポリッシング)はウェーハを平坦にするために削る工程です.研磨としてはCMP (Chemical Mechanical Polishing:化学的機械的研磨)が一般です.
CMPはスラリー (研磨粒子と薬液の混合液)を流し,パッドを擦りつけることで物理的な研磨と化学的な反応の両方によって研磨をします.
洗浄
洗浄はその名の通り,ウェーハ表面を洗浄してよごれやゴミを除去する工程です.除去する対象としてはゴミ (パーティクル),金属汚染,有機汚染,細菌,油,自然酸化膜,レジスト剥離の残りなど様々あります.洗浄は工程の間に頻繁に行われます.
洗浄は様々な薬液 (SPM,APM,HP,フッ酸,有機剥離液など)を用いて何回も行われます.また薬液による洗浄後にはリンス工程 (純度の高い水による洗浄)と乾燥の工程が行われます.
洗浄装置で高いシェアを持つメーカーとしてSCREENホールディングス (日本)や東京エレクトロン (日本)があります.
前工程・バックエンド (BEOL)
金属配線
金属の配線は材料によって工程が違います.アルミニウム (Al)はウェーハにAlを成膜後,フォトリソグラフィとエッチングによって余分な箇所を除去します.
銅 (Cu)は上記の工程が難しいため,ダマシンという工程によって配線を形成させます.ダマシンではまず先に回路パターンに従って誘電体 (SiO2など)が形成されます.その後,配線箇所を銅で多めに埋めて,余分な表面部をCMP (Chemical Mechanical Polishing:化学的機械的研磨)によって削ることで銅配線を形成させます.
まとめ
- 半導体製造装置:半導体製造装置は大別してバッチ式と枚様式がある.
- 前工程:集積チップを製造する工程.
- フロントエンド (FEOL):前工程の内,トランジスタ形成までの工程.
- 成膜:膜を形成する工程.CVDやPVDなどがある.
- フォトリソグラフィ:光の照射により回路などのパターンを描く工程.
- エッチング:ウェーハ表面の一部を取り除く工程.
- 不純物注入:ウェーハに不純物を注入する工程.
- アニール (熱処理):イオン注入した後の活性化やダメージ回復を目的として,ウェーハを加熱する工程.
- 研磨:ウェーハを平坦にするために削る工程.CMPが一般的に用いられる.
- 洗浄:ウェーハ表面を洗浄してよごれやゴミを除去する工程
- バックエンド (BEOL):前工程の内,金属を配線する工程.
- 金属配線:金属を配線させる工程.アルミニウムと銅の配線では工程が異なり,銅の配線にはダマシンという工程が用いられる.