半導体のプロセスは半導体チップを製造する前工程と,その後のパッケージ化などをする後工程に分かれます.本記事では後工程について解説していきます.
そのほかの電子回路やプロセス技術は下記からたどることができます。
後工程
半導体のプロセスは半導体チップを製造する前工程と,その後のパッケージ化などをする後工程に分かれます.前工程では各工程を繰り返し行うことで所望の集積チップを製造します.それに対して後工程は各工程は一度のみ行うフローになっています.
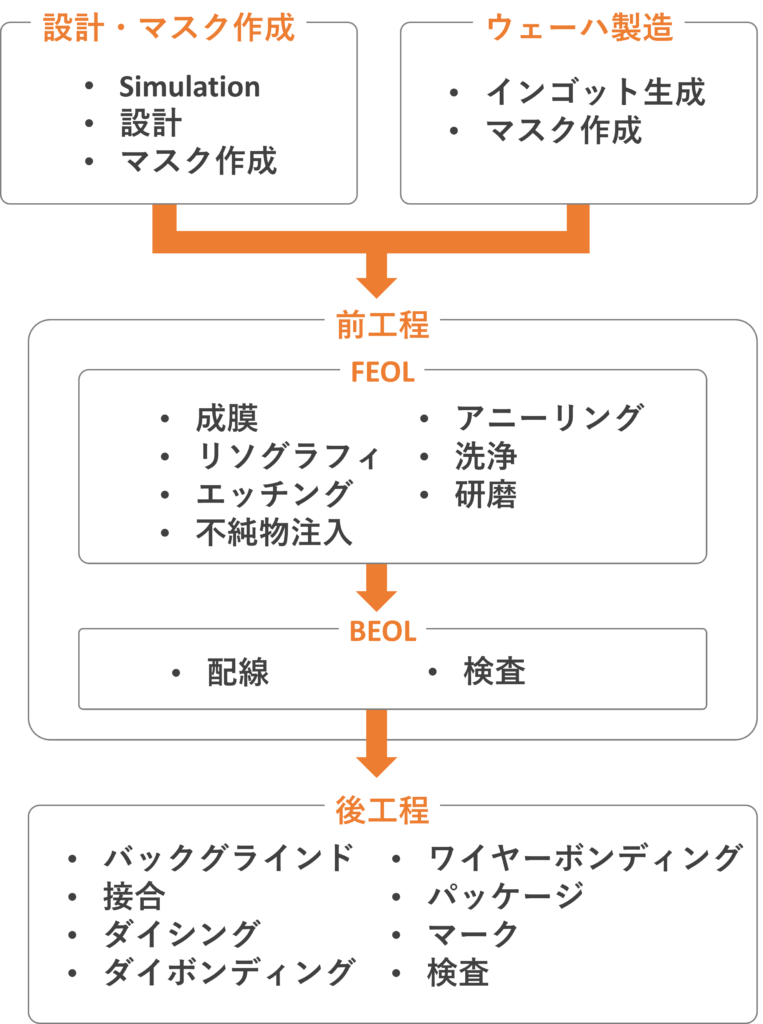
プロービング
半導体プロセスにおけるプロービングは、製造された半導体チップの動作や品質をテストする工程です。このプロセスでは、ウェハ(半導体の基盤)の上にある各回路の接点に微細な針(プローブ)を接触させ、電気的な特性を測定します。これにより、回路が設計通りに動作するか、欠陥がないかを確認できます。
プロービングは、通常、半導体ウェハが切り分けられる前の段階で行われ、各チップが個別にテストされることで、良品と不良品を分けることができます。この工程は、製品の信頼性を確保するために非常に重要であり、不良品を早期に発見して取り除くことができます。プロービングの結果は、後続のパッケージングや実装工程に進むかどうかを決定するための重要な指標となります。
プロービング装置のメーカーとしては東京エレクトロン (日本),東京精密 (日本)があります.
バックグラインド
バックグラインドはウェーハを薄くする工程です.集積チップ製造時はウェーハの強度を上げたり,そりを防止するためにウェーハを厚くしています.しかし,集積チップを使うユーザーは高密度に実装したいため,なるべく薄いウェーハを望みます.このギャップを埋めるために後工程でウェーハを薄くします.
バックグラインドは回路面を保護シートで覆って,ウェーハの裏面をダイヤモンドホイールによって削ります.その際には水で冷却しながら行います.バックグラインドは粗研削,仕上げ研削,ポリッシングとステップを踏んで薄くすることで,欠陥を減らして不良品を少なくなるようにします.
バックグラインドで使用される装置で高いシェアを持つメーカーはディスコ (日本),東京精密 (日本)があります.
ダイシング
ダイシングは、半導体製造プロセスにおける重要な工程で、ウェハ(半導体基板)を個別のチップ(ダイ)に切り分ける作業です。ウェハは、複数の半導体チップが並んでいる大きな円盤状のシリコン基板であり、ダイシングによってこれらのチップが切り出され、最終的に個別の半導体デバイスとなります。
この工程では、ダイシングソーと呼ばれる高精度な切断機を使用して、ウェハ上のチップを切り分けます。ダイシングソーは非常に細かい刃を使い、高速で切断を行いますが、切断中に発生する熱や応力によってチップが割れたり、欠けたりしないように細心の注意が必要です。最近では、レーザーやワイヤーソーを使用した方法もあります。
ダイシングは、チップの性能や品質に影響を与えるため、非常に重要な工程です。切断後のダイは、パッケージングや組み立てに進む前に検査され、欠陥のない良品だけが次の工程に進みます。
ダイシングは以下の3種類に大別されます.
- ブレードダイシング:ブレードを回転させてウェーハを切断
- レーザーアブレーションダイシング:高エネルギーのレーザーを小さい面積に照射して,照射部を蒸発・昇華させることを切断
- レーザーステルスダイシング:ウェーハ内部にレーザー光を集光させて改質層を形成させたあと,外力で切断させる
ダイシング装置でシェアの高いメーカーにディスコ (日本),東京精密 (日本)があります.
ダイボンディング
ダイボンディングは、半導体プロセスにおける重要な工程の一つで、チップ(ダイ)を基板に接続する作業です。この工程では、切り出された半導体チップをパッケージ基板に正確に配置し、電気的な接続を確立するために金属ワイヤやボールで接続します。
まず、ダイボンディング機械は、半導体チップを高精度で基板上に配置します。その後、金属の接続点を使って、チップと基板を接続します。接続方法には、金属ワイヤを使用したワイヤボンディングや、フリップチップ技術を用いることもあります。これにより、チップと基板の間に電気的接続が確立され、チップが正しく機能できるようになります。
ダイボンディングは、製品のパフォーマンスや信頼性に直接影響を与える重要な工程です。適切に行われないと、接続不良やチップの破損、さらには故障につながるため、非常に精密な作業が求められます。
ダイボンディング装置メーカーにBESI (オランダ),ASM (オランダ)などがあります.
ワイヤーボンディング
ワイヤーボンディングは、半導体製造プロセスにおける重要な工程で、半導体チップとパッケージ基板との間に電気的接続を確立するために使用されます。この工程では、非常に細い金属ワイヤ(通常は金やアルミニウム)を使用して、チップの接続端子と基板のパッドを結びつけます。
ワイヤーボンディングでは、まずダイボンディングでチップを基板に配置し、その後、ワイヤーを使用して電気的な接続を行います。ワイヤーは、ボンダと呼ばれる機械で高精度に配置され、圧力と熱を加えることで接続点が確実に結びつけられます。これにより、チップの端子と基板上の回路が電気的に接続され、信号や電力がチップから基板へ、またはその逆に流れることができるようになります。
ワイヤーボンディングは、高速な製造プロセスであり、比較的低コストで行うことができるため、広く使用されています。しかし、接続の品質が製品の信頼性に直結するため、非常に精密な作業が要求されます。
モールド (封止)
モールドは、半導体製造プロセスにおいて、完成したチップを保護し、外部と電気的に接続できるようにするための工程です。この工程では、半導体チップをパッケージ内に封入し、外部の環境からの衝撃や湿気、塵などからチップを保護します。
モールド工程では、まずチップが基板に取り付けられ、ワイヤーボンディングで接続された後、次にパッケージの上部にモールド材(通常はエポキシ樹脂など)を注入します。これにより、チップ全体が封じ込められ、外部からの物理的なダメージから保護されます。また、モールド材は熱伝導性を持ち、チップの熱を効率的に外部に放出する役割も果たします。
モールドは、半導体パッケージの耐久性や性能に直接影響を与えるため、非常に重要な工程です。適切にモールドが施されていないと、チップが破損したり、信号が不安定になったりする可能性があるため、精度と品質が求められます。
まとめ
- 後工程:前工程でトランジスタなどが形成されたウェーハをパッケージ化までをさせる工程の総称
- プロービング:各チップを電気針で正しく動作するかを確認する工程
- バックグラインド:ウェーハを薄くする工程
- ダイシング:チップを一つずつ切り出す工程
- ダイボンディング:集積チップと支持体を接続させる工程
- ワイヤーボンディング:集積チップとパッケージを金属で接続する工程
- モールド (封止):パッケージを樹脂などで封止する工程